In the food manufacturing industry, in addition to the conventional challenges of achieving both "ensuring food security and safety" and "cost reduction," manufacturers are also working to cope with infectious diseases and labor saving.
YOKOGAWA supports manufacturers to create comfortable workplaces by working closely, coping with challenges together, and proposing ideal factories suitable for operations.
Smart Factory/IIoT
Transform a food and beverage factory into a smart factory using the IIoT to automate the entire facility, manage all information in a centralized manner, and reduce costs throughout.
Cost Reduction
Enable cost reductions through detailed cost variance analyses, which link information on production, sales, and inventory, while automatically collecting manufacturing statistics.
Traceability
Certify the results of error-free manufacturing and quickly respond to customer inquiries.
Quality Management
Improve the reliability and efficiency of QM through automatic data recording, paperless management, and standardized inspection procedures.
Food Defense
Ensure safety and security by preventing unauthorized personnel from entering the factory and foreign materials from entering production lines.
HACCP / FSSC22000
Satisfy HACCP requirements and regulations such as FSSC 22000 while discovering solutions to address food safety and sanitation management.
Equipment Maintenance
Detect equipment malfunctions, predict failures, and develop maintenance plans to optimize operations.
Energy Management
Provide visualization of energy consumption, awareness of energy inefficiencies, and energy use-improving activities that can reduce costs.
Sensors for Food Factories
Support food and beverage safety and security by substantially expanding accurate measurements throughout the factory.
Details
Smart Factory/IIoT
Smart factory as envisioned by YOKOGAWA
Smart factory as envisioned by YOKOGAWA is a factory in which various data on 4Ms (Machine, Man, Material, and Method) in a food factory are centrally managed, factory automation and labor saving are promoted, and the following three points are realized.
- Improvement of quality and productivity
- Cost reduction by reducing losses incurred in manufacturing and indirect operations
- To create an environment in which more value-added work can be concentrated
Instead of partially introducing automated equipment, the entire factory can be optimized by connecting equipment and data through IIoT utilization within the factory and constructing a foundation.
In the food manufacturing industry, in addition to the conventional challenges of achieving both "quality improvement" and "cost reduction," flexibility is required to respond appropriately to the following new challenges.
- Shift to low-volume production of multiple products due to diversified consumer needs
- Decline in working population and the succession of skills
- Adaptation to the New Normal Era (breaking out of manufacturing sites' crowded situation/manpower-based production)
To achieve the above objectives, YOKOGAWA is advocating the IA2IA (Industrial Automation to Industrial Autonomy) initiatives.
IA2IA means a shift to a manufacturing system that realizes "autonomy of operation" where the system is responsible from startup to shutdown by breaking away from processes that require constant human monitoring and interventions and where facilities learn and adapt by themselves.
For details, see the following link.
⇒ Industrial Automation to Industrial Autonomy
YOKOGAWA's consulting services
YOKOGAWA provides comprehensive consulting services by combining a variety of products based on its experience and expertise over many years and helps customers realize their smart factories.
For details, see the following link.
⇒Consulting
Effects:
(1) Automatic planning of production plans reduces the number of planning processes and eliminates dependence on individual skills
(2) Achieve unification and visualization of cost data, and clarify points that require cost reduction measures
(3) Reduce inventory loss through accurate raw material management in response to multi-product production
(4) Establishment of sign monitoring/preventive maintenance infrastructure reduces equipment downtime, number of failures, equipment restoration time, and production opportunity loss
(5) Prevention of incorrect input and reduction of incorrect work loss in multi-product production by double-checking by personnel and the system
(6) Achieve rapid traceability by integrating production results
(7) Reduce analysis time and implement quick quality stabilization measures by integrating inspection results
(8) Production process automation/labor saving for workers and reduction of on-site personnel achieved through control of production processes, equipment, and robots
(9) Identify and improve wasted energy by unifying energy consumption and facility operation results for each facility
(10) Collection/analysis of operation data achieves debottlenecking and quality stabilization
Major Package Products for Smart Factory Construction and Effects
Solutions | Package Product Name | Effects |
---|---|---|
【Production scheduling】 | Production Scheduler FLEXSCHE | (1) |
【Production, sales and cost management】 | Production Management mcframe | (2)(3) |
【Equipment maintenance and management】 | Computerized Maintenance Management System eServ | (4) |
【Failure prediction and management】 | Automatic Device Status Analysis Package DUCSOnEX Predictive detection |
(4) (4) |
【Manufacturing execution and management】 | Manufacturing Management Package CIMVisionLIBRA |
(3)(5)(6)(8) |
【Quality/inspection management】 | Laboratory Information Management System LIMS | (7) |
【Logistics/warehouse management】 | Logistics Management Package MaterialStream | (3)(8) |
【Process database】 | Realtime Operational Information Management Package PI System Plant Information Management System Exaquantum IIoT Solutions for Efficiency Process Data Analytics Quality Stabilization System [Digital Plant Operation Intelligence] |
(9) (9)(10) (7)(10) (7)(10) |
【Energy management】 | Factory Energy Operation Supporting System Enerize E3 Energy Management |
(9)(10) (9)(10) |
【Procedural Automation】 | Operation Efficiency Improvement Package Exapilot | (5) |
【Production process monitoring and control】 | Distributed Control System (DCS) CENTUM VP Field Instruments |
(8)(10) (8)(9)(10) |
Solutions Map
※Some of the products introduced may differ between the Japanese version HP and the English version HP.
Cost Reduction
Cost reduction is achieved through the following five points: (1)production planning support; (2)production management and cost management; (3)equipment maintenance; (4)manufacturing management; and (5)automated control and quality-stabilization
(1) Production Planning Support
Challenge
- Production planning by manual work takes time and labor
Solutions
- Automatic planning of the production plan considering people, equipment, and contamination is possible
- Highly visible user interfaces facilitate progress management of planned plans
Effects
- Realize sharp reduction of planning man-hours, shortening of planning time, and elimination of dependence on individual skills
- Realize reductions in production costs, opportunity losses, and in-process inventory through efficient planning in line with operations
(2) Production management and Cost management
Challenges
- Difficulty in calculating costs such as profit analysis and cost variance analysis
- Difficult to grasp accurate costs, results, and losses
- Manufacturing is unable to follow changes in sales plans due to demand fluctuations
Solutions
- Accurate performance data collection from manufacturing sites and cost accounting enable grasping of costs and losses
- Achieve response to fluctuations in supply and demand through collaboration between manufacturing, sales, and inventory information, as well as high-speed MRP
- Planning that reflects production conditions enables smooth reflection of plan revision to manufacturing sites
Effects
- Realize cost reductions by setting standard costs, grasping actual costs, and simplifying cost variance analysis
In addition, realize reduction in man-hours required for the above-mentioned work - Reduce production opportunity losses by promptly responding to changes in supply and demand
- Reduce inventory losses through appropriate inventory management
(3) Equipment Maintenance
Challenges
- A sudden facility failure has resulted in line shutdown, time for restoration required, and loss of opportunity
- Maintenance parts management cannot be performed correctly, resulting in excessive parts inventory
- Regular inspections to prevent sudden breakdowns lose touch with the actual state of breakdowns and lead to excessive inspections, resulting in a shortage of man-hours
- It takes time to plan and review the inspection plan
Solutions
- Integrated management of information related to equipment maintenance, such as past failure data, and prompt formulation of inspection plans
- Cooperation between centrally managed information and facility operation data enables CBM and eliminates surplus inspections
- Continuous monitoring of equipment vibrations and temperatures enables detection of equipment malfunctions and precautions against failures without periodic inspections
※CBM:Condition Based Maintenance
Effects
- Stable operation of facilities realizes production as planned and reduces losses due to waste loss
- Realization of CBM reduces equipment shutdown time, number of failures, and equipment restoration time
- Reduce maintenance management man-hours, such as paper management and transcription, by centralized management of information
- Efficient facility inspection and reduction of inspection man-hours by sign monitoring
(4) Manufacturing Management
Challenges
- First-in, first-out management of raw materials is not properly implemented, and waste loss is generated
- Disposal loss due to work errors such as incorrect weighing and incorrect input
- Tracing in the event of quality abnormalities, facility troubles, or work errors takes a long time, and prompt response is not possible
- The automation facility has been introduced, but man-hours of workers can not be reduced
Solutions
- Achieve appropriate reserve management and accurate inventory management from receipt to use-up
- Realize computerization of information such as on-site results manually managed by paper etc.
- Manage standard operation procedures by the system, and realize guidance of procedures and double-checking by the system and personnel
Effects
- Reduce raw material inventory by improving inventory control accuracy and reducing expired materials
- Electronization of site performance information realizes tracing time reduction and prevention of inconsistency with inventory information due to transcription errors
- Reduce work errors by workers and reduce waste loss
- The system supports instructions to automation equipment and achieves overall manufacturing site optimization
(5) Automated Control and Quality-Stabilization
Challenges
- Automated equipment has been introduced, but it takes time to adjust for each manufacturing item
- The quality is not stabilized, and the cause is not known
- Inefficient production due to line shutdowns and deviated supply timing of materials etc. caused by equipment abnormalities
Solutions
- Realize automatic control based on recipes that have reached manufacturing items through the introduction of DCS
- Stabilization of quality by the measure of visualizing 4Ms fluctuation factors
- Monitoring the signs of equipment malfunctions and realizing JustinTime manufacturing through the cooperation of automated equipment and materials supplies
Effects
- Shorten downtime when changing manufacturing items
- Achieve optimal operation by ensuring stable quality while following changes in manufacturing sites
- Reducing production line shutdowns and achieving stable plant operations
An example of how a production/cost management system can be used for cost reduction
You can get greater effects of cost reduction by implementing a production management and cost management system,
enabling cost visualization and cost variance analysis, and implementing targeting activities for cost reduction
Major Package Products for Cost Reduction and Challenges
Package Product Name | Challenges |
---|---|
Production Scheduler FLEXSCHE | (1)(2) |
Production Management mcframe | (2) |
Computerized Maintenance Management System eServ | (3) |
Automatic Device Status Analysis Package DUCSOnEX | (3) |
Manufacturing Management Package CIMVisionLIBRA | (4) |
Operation Efficiency Improvement Package Exapilot | (4) |
IIoT Solutions for Efficiency Process Data Analytics | (5) |
Quality Stabilization System [Digital Plant Operation Intelligence] | (5) |
Distributed Control System (DCS) CENTUM VP | (5) |
※Some of the products introduced may differ between the Japanese version HP and the English version HP.
Traceability
In the food manufacturing industry, everyone may probably be working to establish a food chain that provides even "safer" and more "secure" products.
With established traceability, YOKOGAWA supports food manufacturers by immediately tracing back the production results to determine the causes of any inquiries about the products after shipment and to enable prompt responses to such inquiries.
Environment surrounding food production
Due to heightened health awareness, the introduction of risk-management systems such as HACCP, and the need for food diversity, interest in food "safety" is rising, and "quality" requirements are becoming more stringent not only for the food manufacturing industry, but also for companies involved in food products.
Allergen issues
- What are the contained allergens?
- Is the allergen content of raw materials/production materials acceptable?
- Is there a possibility of allergen contamination?
Halal certification
- Are they compliant with Halal certification?
Challenges in the Food Manufacturing Industry
- Rapid response to inquiries from the market
(establishment of a system for responding to inquiries and indicated items) - Quick response to quality problems caused by abnormalities in raw materials and manufacturing processes
Integrated management of information from development to manufacturing and from manufacturing to supply
(Establishment of a Trace Forward/Traceback System) - Shortened life cycle of products:
A large amount of information needs to be managed due to the small-scale production of a wide variety of products
YOKOGAWA's traceability solutions
Traceability systems are classified into production traceability systems and distribution traceability systems.
YOKOGAWA provides solutions primarily related to traceability in production.
Using production management systems and manufacturing management systems, we realize integrated management of information about manufacturing and support a range of operations from procurement to manufacturing and shipment.
In addition to responding to inquiries from consumers, we provide quality management and quality assurance solutions aimed at creating quality that supports food "safety" and "security."
(1) Production Management:
Managing production plans and raw material procurement plans, such as what to make and when, and to what extent
(2) Manufacturing Management:
Assisting to prevent work errors such as incorrect input, and managing production results such as what was made and how it was made
(3) Quality Management:
Management of quality data such as analytical values and cleaning records in the inspection of raw materials and products
(4) Equipment Maintenance:
Management of equipment conditions such as temperature in the manufacturing process
Major Package Products and Solutions for Building Traceability Systems
Package Product Name | Solutions |
---|---|
Production Scheduler FLEXSCHE | (1) |
Production Management mcframe | (1) |
Manufacturing Management Package CIMVisionLIBRA | (2) |
Operation Efficiency Improvement Package Exapilot | (2) |
Laboratory Information Management System LIMS | (3) |
Realtime Operational Information Management Package PI System | (4) |
Plant Information Management System Exaquantum | (4) |
Panel Mount Recorders Touch Screen GX10/GX20 | (4) |
※Some of the products introduced may differ between the Japanese version HP and the English version HP.
Food Defense
Total food defense to strengthen security on food factory premises and in factories
Contamination in the factory is one of the major causes that undermine confidence in the company.
In order to protect against deliberate contamination of food products, YOKOGAWA is developing mechanisms to prevent food products from becoming contaminated before something happens and to track food products after it happens, and supports food production sites to protect food safety.
- Access control :Entrance to the premises only by the parties concerned
- Entrance and Exit control : Entry into the factory and entry into the manufacturing process by only related persons.
- In-process monitoring : Control of traceability of raw materials/products and video recording of in-process operations
In order to strengthen food safety and security, we also support food safety perspectives such as appropriate temperature and hygiene control.
For details, see the following links.
Traceability / HACCP
COVID-19 countermeasures
In recent years, the outbreak of COVID-19 has forced the food manufacturing industry to take various measures, such as controlling the physical condition of field workers and avoiding the three Cs (Closed spaces, Crowded places, and Close-contact settings) at factories.
We provide a temperature measurement solution that can detect the temperature of many people at a time safely and speedily and can track individuals.
This solution can identify individuals early who have developed a fever and support measures to prevent disease clusters from occurring at factories.
Supporting the acquisition of Food Safety Systems Certification Standard FSSC22000
Following recent social trends, there is an increasing number of cases where suppliers are requested to obtain certification for food safety and hygiene management standards.
We assist in addressing the requirements of Food Defense, Biovigilance and Bioterrorism, described in Chapter 18 of Prerequisites Program ISO/TS22002-1: 2009 for Food Safety Systems for Food Manufacturing FSSC 22000.
Defense in the manufacturing process
|Access control | Recording of work videos | In-process zoning control | Ingredient/Chemical storage linking |
Access control
Card/fingerprint authentication system prevents outsiders from entering.
Surveillance cameras also monitor intrusion from outside.
Recording of work videos
Using the Manufacturing management system , the operation of inputting raw materials is recorded with the direction of web cameras changed to the input port timely.
In-process zoning control
Establish a system to detect entering and exiting in the production process and not allow anyone other than those concerned to enter the room.
- Management of staying hours:If staying time exceeds the preset time, it is judged to be abnormal
- Anti-pass back:This function prevents entry and exit without card operation
If you do not follow the procedures of "Entry" and "Exit," it is judged unauthorized use of the card
Ingredient/Chemical storage linking
Image detection technology detects the removal of goods from the raw material and chemical warehouses and records the images.
Major Package Products for Food Defense
- Manufacturing Management Package CIMVisionLIBRA
- Operation Efficiency Improvement Package Exapilot
- Monitoring camera FIELDEYE
※Some of the products introduced may differ between the Japanese version HP and the English version HP.
HACCP / FSSC22000
This section introduces hygiene management solutions at food factories, such as those for HACCP, for FSSC22000*, for food quality management, and for sanitary equipment, as well as efforts to reduce food loss.
*FSSC22000: International Standard for Food Safety Management Systems
Complying with HACCP Requirements
The introduction of HACCP is expanding year by year in many countries worldwide.
As imports and exports of food become increasingly active in the future, HACCP, a method of managing international standards, is crucial for maintaining food safety.
In accordance with the Guideline of 7 principles and 12 steps stipulated by the Codex Alimentarius Commission, it is required to monitor and control the process from stocking raw materials to supplying products.
YOKOGAWA supports HACCP compliance from the standpoint of Step 6: Conducting a hazard analysis, Step 7: Determining Critical Control Points, Step 9:Establishing monitoring system, Step 10:Establishing corrective actions, Step 11:Establishing verification procedures, and Step 12: Establishing documentations & record keeping.
Efforts to Reduce Food Loss
As food loss reduction has become an issue worldwide, food-related businesses are required to take measures to reduce food loss, such as using raw materials without waste and extending the shelf life of products.
YOKOGAWA supports efforts to reduce food loss from the perspectives of "quality-risk reduction" and "appropriate inventory control".
Sanitary Sensor and Analyzer
YOKOGAWA provides sanitary sensors and analyzers to meet stringent hygiene requirements for the food manufacturing industry.
Major Package Products for Ensuring Food Safety
- Manufacturing Management Package CIMVisionLIBRA
- Operation Efficiency Improvement Package Exapilot
- Laboratory Information Management System LIMS
- Realtime Operational Information Management Package PI System
- Plant Information Management System Exaquantum
- Panel Mount Recorders Touch Screen GX10/GX20
※Some of the products introduced may differ between the Japanese version HP and the English version HP.
Equipment Maintenance
YOKOGAWA provides solutions to preventing failures, factory stability, safe operation, and reducing production opportunity loss, including an equipment maintenance system that supports facility ledger management and maintenance planning, as well as a machine learning-based abnormal prediction detection system.
(1)Equipment maintenance system that supports maintenance operation
Challenges
- The optimal replacement cycle of equipment parts is unknown, and the inspection cycle is unknown
- It takes time to respond to restoration by a sudden drop in performance of production equipment or stoppage
Solutions
- Visualization of fault history enables to determine the replacement cycle of equipment parts and create an optimal maintenance plan
- Integrated management of equipment-related data ensures proper equipment spare parts inventory control
Effects
- Reduction in man-hours through review of periodic inspection work
- Reduce sudden equipment failures and reduce production opportunities loss
- Unified management of equipment and maintenance information reduces indirect operations such as paper management and transcription
- Reduction in the time required to respond to equipment problems
(2)Equipment maintenance by detecting signs of abnormal conditions
Challenges
- Major opportunity loss was caused by a sudden failure or line stoppage of production equipment
- Detection of abnormalities in production equipment was delayed, forcing product disposal and recall
Solutions
- Detecting minor abnormalities in equipment and raising the alarm before a failure occurs enables prevention of failure
- Continuous monitoring of equipment vibration and temperature to detect signs of equipment malfunction
- Analysis of collected data enables quick identification of the cause of failure
Effects
- Reduce sudden equipment failures and reduce production opportunities loss
- Reduce quality risks caused by equipment and process abnormalities
- Reduction in the time required to respond to equipment problems
Major Package Products for Equipment Maintenance and Challenges
Package Product Name | Challenges |
---|---|
Computerized Maintenance Management System eServ | (1) |
Industrial IoT Data Logging & Dashboard | (2) |
Sushi Sensor | (2) |
Automatic Device Status Analysis Package DUCSOnEX | (2) |
Predictive detection | (2) |
Data Logging Software GA10 | (2) |
※Some of the products introduced may differ between the Japanese version HP and the English version HP.
Energy Management
Visualization of energy consumption not only realizes energy savings, but also helps improve operations by discovering waste and dispersion.
Challenges:
- difficulty in identifying improvement points for energy management
- Energy management is being promoted, but we don't know what to do next
- In addition to saving energy in utilities, we want to link with production processes to reduce overall production costs
Solutions:
- Support for discovering waste and setting the optimal KPI
- Energy consumption rate per product and lot realizes clarification
- Realize support for energy conservation activities throughout the entire production process by integrating energy information and production information
Effects:
- Visualization of energy consumption throughout the plant enables monthly comparison and identification of improvement points
- Investigation of energy-saving measures and measurement of effects can be made easier by grasping the trends of each line
- Linking with production information enables analysis of the causes of energy efficiency deterioration in the manufacturing process.
- Comparison of the same manufacturing item with other factories enables optimal production planning from a utility cost perspective
YOKOGAWA's Kofu factory, located in Japan, has achieved significant results in energy-oriented improvements, focusing on the IT-based visualization system and the systematic operation, and has attracted attention as a model plant for energy management.
For details, see the following link
⇒Kofu factory
Major Package Products for Energy Management
- Production Scheduler FLEXSCHE
- Factory Energy Operation Supporting System Enerize E3
- Energy Management
- Data Logging Software GA10
※Some of the products introduced may differ between the Japanese version HP and the English version HP.
Sensors for Food Factories
Major sensor products for food factories
■Sanitary sensor
■Other sensors
- Distributed Temperature Sensor
- Tunable Diode Laser Spectrometers
- Sushi Sensor
- Level Meters
- Magnetic Flowmeters
- Vortex Flowmeters
- Coriolis Mass Flowmeters
Application example of Coriolis mass flowmeter
We change the common sense that "foam" in the mass flowmeter is not good.
Challenge
- If air bubbles enter the existing mass flow meter it becomes over range
Solution
- Measurement is possible even for fluids containing 10% or more bubbles
Effect
- Continuous measurement is possible, which reduces the loss of products discarded due to unknown blending volume due to bubble contamination
※Some of the products introduced may differ between the Japanese version HP and the English version HP.
※Please note that the mounting port differs depending on the area and the standard.
Through extensive experience built on long-term relationships with IA industry leaders, Yokogawa offers the advanced products and custom solutions that food and beverage manufacturers need to create a quality product. Brewery operations and sugar manufacturing serve as two examples.
| Brewing Applications | Sugar Production Applications |
Brewing Applications
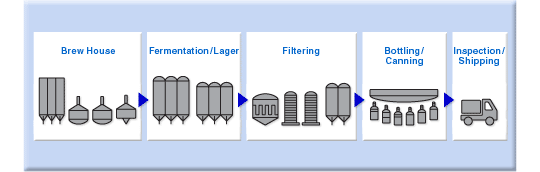
Malt Silo
- Raw Material Handling
Brew House
- Raw Material Handling
- Mashing
- Batch Management
- CIP (Cleaning In Place)
Fermentation/Lager
- Fermentation/Lager
- Racking
- Fermentation Management
- Yeast Management
- CIP (Cleaning In Place)
Filtering
- Filteration
- Beer Movement
- CIP (Cleaning In Place)
Bottling/Canning
- Packaging
- Warehousing
Inspection/Shipping
- Quality Control
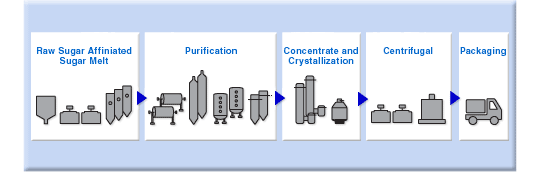
Affiniated Sugar Melt
- Weighing Control
- Affination
Purification
- Carbonation
- Filter Machine Control
- Ionic Exchange Resin Control
- Decolourization
Concentrate and Crystallization
- Concentration
- Vacuum Pan Control
- Centrifuge Control
Centrifugal
- Drying Control
Packaging
- Packaging Management
Resources
Shree Renuka Sugars Limited (SRSL) is a global agribusiness and bio-energy corporation. The company is one of the world’s largest sugar producers and refiners.
NISSIN FOOD PRODUCTS selected Yokogawa as a partner to realize a next-generation smart factory.
An integrated MES solution helps fully automate the large-scale food factory in Japan.
- Yokogawa provided control solutions for expansion project in sugar and bio-energy plant.
- Consolidated central control room was designed for safe, comfortable, and efficient work environment.
S&B Sankyo uses the GX20 Paperless Recorder to monitor temperature and pressure in a food processing plant's sterilization process.
Since Mannan Life not only suffered significant loss due to line shut down or disposal loss from unexpected operation problems, but were also often pressed with support work such as arranging personnel, materials, and equipment for repair or after-the-fact processing, how to prevent operation problems was a major issue for management.
To solve this problem, with the second year of introduction as a target, the Kanra Factory began working to shift its work to preventive maintenance, which prevents machine failures and line shut downs due to machine degradation over time.
Rousselot Ghent won Belgium Factory of the Future Award. Yokogawa has supported Rousselot with automation systems since 1993.
Data of 20,000 tags gathered by Exaquantum helped to find the ideal production parameters.
The Pasteurized Milk Ordinance (PMO) is a set of standards and requirements that regulate aspects of dairy plants producing Grade “A” products. It is the “dairy bible” that dairy producers, manufacturers, and balancing plants must follow to verify food safety. Discover how Yokogawa recorders (PMO compliant) are helping Michigan milk producers.
Kyowa Hakko Bio monitors vibration trends with Yokogawa's Sushi Sensors to prevent unexpected equipment failures.
By using eServ, sensor data and maintenance information are shared with everyone involved in manufacturing.
The introduction of eServ has resulted in a centralized system of facility information. The reason for the loss of production opportunities has become clear, and it has become possible for all members to follow up the progress of the measures.
KIRISHIMA SHUZO is the top sales shochu company in Japan for the fourth straight years.
We systematized both cost and manufacturing management, and aimed to achieve maximum cost reductions by utilizing these two systems.
DTSX solutions for brewery
Detection of a clogged shower in pasteurization process
Improving customer satisfaction and protecting brand value requires a relentless commitment to quality. Understanding the status of beer yeast is key to improving quality and manufacturing products that taste the same.
The TC series of temperature controllers is perfect for controlling the heating temperature of sealing parts and the temperature of sealing rolls (pre-heating) in a variety of different wrapping machinery.
- The new package software running on the CENTUM CS 3000 has enabled flexible configuration and data settings for greater productivity.
- The CENTUM CS 3000 features a standard long-term trend function that can store a year's worth of data on more than 200 tags that are sampled at 2 minute intervals.
In the past, the boiler feed tank systems in sugar factories had to be checked several times a day to make sure there were no sugar solution leaks. This was a very laborious process and, as continuous monitoring was not possible, monitoring results were not reliable. When a leak occurred, recovery operations were very costly and time-consuming. (AN10D01K01-02E)
- For remote monitoring (of temperature, pressure, and flow volume), installing the SMARTDAC+ GM in the plant and the SMARTDAC+ GX in the office provides for a scalable, pc-free on-site data monitoring solution.
- You can centralize management of large quantities of data by automatically transferring acquired data to a FTP server.
One of the critical control points in the brewing process is the monitoring of the progress of the fermentation stage. The DM8 Vibration Type Liquid Density Meter offers high sensitivity and stability, realizes precise control, reduces workload, and reduces instrument costs.
Skim milk is what remains after cream is removed from raw milk. Cream is removed to bring the fat content of the skim milk as close as possible to the lower limit of a designated range. For this purpose, control of the fat content in the cream and the skim milk is essential. The fat content in the cream and the milk has a direct relationship to their density and is controlled by the measurement thereof.
SMARTDAC+ GX series records the clean room temperature, humidity, atmospheric pressure, door openings and closings, etc.
The discharge of improperly treated industrial chemicals and fuel gas can have a major impact on the environment, posing a serious threat to public health. Concurrent with the global growth of manufacturing operations to keep pace with market trends, many countries are taking measures to deal with environmental problems.
Milk should be processed within 4 to 6 hours of production to make it fit for human consumption. Temperature is a very important parameter which has to be monitored at different stages of milk processing.
In the plants of food and beverage manufacturers, there are times when monitoring and recording of production equipment is necessary inside clean rooms. This is an introduction to monitoring and recording in clean rooms using paperless recorders.
Yokogawa's ceramic liner can offer the customer superior resistance to thermal shock and the failure that can occur due to liner cracking. This is due to Yokogawa's use of 99.9% pure Al2O3 for the liner.
Brewery is facility to produce beer. Breweries process is the manufacturing process of beer, which is a fermented beverage with low alcohol content made from various types of grain. Wheat, maize and other grains can be used for this. Brewing process starts from malted barley that is to form a mash by milling and mixing with hot water. The malt starches are converted to sugars during this process. This sugar rich water is then strained through the bottom of the mash and will be called as "wort". Then the wort will be brought to boil by bringing to the brew kettle. For bitterness or aroma hops are to be added at different times during the boil. Then the wort is cooled and aerated. And brewers yeast is added for fermentation. From the sweet wort the yeast produces carbon dioxide, alcohol and other byproducts. The GREEN BEER undergoes maturation after fermentation. Filtaration and carbonation are the last steps. Finally the beer will be stay in holding tank until it is bottled or kegged.
How automated real-time noise map can contribute to production efficiency
The paperless recorder DX series automatically calculate the Fo value from the heating temperature and are useful in managing the sterilization process by displaying and recording the value together with the heating temperature.
Monitoring of Soundness of Power Supply Bus Bar (In-vehicle Lithium-ion Battery Applications)
In the food industry, the control of concentrations on the production line is critical to product quality, determining, among other things, how good the food tastes. One such procedure for doing this involves taking a sample from the production process and measuring its specific gravity (density) with a hydrometer.
By using the Multibatch function (an option added with SMARTDAC+), you can efficiently record data from multiple devices onto a single SMARTDAC+.
Using the custom display function that comes standard with DXAdvanced means that you can combine the recorders, displays, and switches used in various kinds of equipment.
Using the batch name + lot number system, past measured data can be recalled for reference by batch name.
- Universal inputs provide support for thermocouple, RTD, voltage, and a variety of other input signals.
- Lineup of models for up to 450 inputs.
Allows multipoint monitoring and recording on a single unit. - Easily enables network-based data management.
file transfers, Web monitoring, and alarm e-mail
By using the computation function of the SMARTDAC+ series Paperless recorder GX/GP, computation option computes the "F-value," or sterilizing value for the sterilization process, so that the computation results can be recorded in the form of data.
With industrial and economic development comes increasingly large and advanced power plants and factories. Nevertheless, we find many cases where the original cables, cable tunnels, and other components of the power infrastructure have languished under continuous operation.
The sterilization temperature prior to the filling process is monitored in the field or office. The temperature data is recorded in an external storage medium.
Fish perform all their bodily functions in water. Because fish are totally dependent upon water to breathe, feed and grow, excrete wastes, maintain a salt balance, and reproduce, understanding the physical and chemical qualities of water is critical to successful aquaculture. To a great extent water determines the success or failure of an aquaculture operation.
This introduces a system that uses Ethernet communications to acquire measured values, target values, and control output values from a controller installed on site into a PLC at high speed (ten units' worth within one second).
To defray energy costs, many industrial plants have their own boilers to generate steam in order to produce a portion of their energy needs. In addition to generating power, the steam may also be used directly in plant processes or indirectly via heat exchangers or steam jacketed vessels.
With advances in process automation comes a greater need for level measurement and control. As pressure on at the bottom surface of a liquid is proportional to the height of the liquid's surface, you can measure pressure using a differential pressure transmitter to detect the level of the liquid, acquire the data on the UT75A Digital Indicating Controller, and use the measurements to control the tank level.
In the manufacturing process of Pharmaceutical, Chemical and Food & Beverage industries, the cleaning and sterilization of tanks and piping are done with various cleaning solutions, fresh or hot water and steam after manufacturing products. Clean-In-Place (CIP) is the system designed for automatic cleaning and disinfecting.
Reverse osmosis (RO) is a separation process that uses pressure to force a solution through a membrane that retains the solute on one side and allows the pure solvent to pass to the other side. More formally, it is the process of forcing a solvent from a region of high solute concentration through a membrane to a region of low solute concentration by applying a pressure in excess of the osmotic pressure.
After extraction from sugar cane or sugar beets, juice must be purified to remove the many other organics and minerals that accompany it. The processing to accomplish this is heavily dependent on reliable pH measurement and control as illustrated.
One of the primary applications for high purity water is for boiler feed water. The measurement of pure water pH can be one of the quickest indicators of process contamination in the production or distribution of pure water. Effective chemical treatment of the feed water is vital in maintaining the useful operating life and minimizing maintenance costs of the boiler.
Industry:Power, Pharmaceutical, Common
Optimizing four key factors will decrease pH sensor costs and optimize process control and overall plant efficiency.
This technical white paper will discuss Yokogawa's CENTUM VP DCS (Distributed Control System) product, hereafter referred to as "CENTUM VP", and the extent of its compliance with Part 11 of Title 21 of the Code of Federal Regulations, (21 CFR Part 11), the Electronic Records / Electronic Signatures Rule.
Sugar and alcohol market are increasing, due humanity needs to find alternatives for fossil fuels dependence. Brazil joins climactic and technologic features to place itself at the forefront of this industry.
The worlds of process automation and production management have been converging for some time. What once used to be islands of automation and production management functionality connected through highly proprietary integration schemes that were costly to maintain have developed into integrated platforms that provide seamless data exchange between the world of automation and the plant floor, the functions of production and operations management, and integration with business level systems.
The world of process automation is governed by procedures. While we like to refer to the process industries as being largely "continuous", this could not be further from the truth. Process manufacturing is constantly in flux.
This document describes the operation and data flow of the Yokogawa Print Wave software using the DX-P Reporter. It will provide a detailed explanation of the Advanced Alarm Reporter functions. The functions described in this paper were first released in Print Wave version 5.5.
Discovering your Baseline with OT Security Risk Assessment
Honeywell and Yokogawa have both been producing Distributed Control System (DCS) platforms for decades, and both are very active in this area. In 1975, Honeywell introduced its TDC2000 platform and Yokogawa brought out CENTUM. These two competing systems emerged from a similar place, oil refining and petrochemical industries, so they started out with similar basic concepts and use cases in mind.
The use of optical fiber for temperature sensing is expanding beyond safety applications.
The wireless standard LoRaWAN enables wireless communications and digital transformation over long distances, supplementing in-plant wireless networks such as ISA100.
Cloud-based wireless sensing enables safety, reliability, and profits through widespread asset monitoring.
Process automation systems are increasingly connected to IT systems and the outside world, introducing cybersecurity concerns, which can be addressed using techniques such as software-defined networking and monitoring services.
Asset management plays a key role in operational safety, and it is critical to capture and transmit these data in a secure, digitized way to ensure that they are up to date, accurate and easily accessible.
Robots have long been used in discrete manufacturing and machine automation applications, and their use is now spreading to address process industry applications.
Assets and operations will have human-like learning and adaptive capabilities, allowing responses without operator interaction to situations within a secure, bounded domain.
Historians provide the data storage, secure connectivity and built-in tools required for implementation of digital transformation initiatives.
Downloads
Brochures
General Specifications
Certificates
- EU_UK Declaration of Conformity FU20 2022-11-14 (170 KB)
- EU_UK Declaration of conformity SX42 2022-11-14 (152 KB)
- EU_UK Declaration of conformity SC42 2022-11-14 (158 KB)
- EU_UK Declaration of Conformity SC29 2022-11-14 (146 KB)
- EU_UK Declaration of Conformity PR10 2022-11-14 (140 KB)
- EU_UK Declaration of Conformity SM23 2022-11-14 (121 KB)
- EU_UK Declaration of Conformity SC21 2022-11-14 (146 KB)
Videos
The Yokogawa business vision states that the company endeavors to achieve Net-zero emissions, ensure the Well-being of all, and make a transition to a Circular Economy by 2050.
YOKOGAWA will contribute to technology evolution particularly in measurement and analytical tools to help build a world where researchers will increasingly focus on insightful interpretation of data, and advancing Life Science to benefit humanity.
DTSX has been increasingly used in variety of applications such as fire detection, leak detection and preventative maintenance.
YOKOGAWA creates autonomous operations with high-efficiency automation and optimization that allows growth with minimal deployment of manpower.
Our approach is to leverage state-of-the-art technologies for real-time monitoring and predictive control that allow virtual environments where "digital twin" processes can provide distinct advantages.
News
-
Press Release Jun 22, 2023 Yokogawa to Release OpreX Informatics Manager, Enabling Integrated Management of Experimental Data and Research Resources in the Cloud
-
Press Release Feb 13, 2018 Yokogawa Releases Operations Management Software Package
- Optimizes the supply chain and operations by enabling plant personnel to work more efficiently -
-
Press Release Dec 18, 2017 Yokogawa Develops N-IO Standard Field Enclosure and Control System Virtualization Platform
- For improved agility in implementing control system projects -
-
Press Release Dec 4, 2017 Yokogawa Releases FAST/TOOLS R10.03 Web-based Real-time Enterprise Operations Platform
-
Press Release Nov 21, 2017 Yokogawa Releases ISA100 Wireless Gateway Module
- Ideal for construction of small-scale field wireless systems -
Looking for more information on our people, technology and solutions?
Contact Us